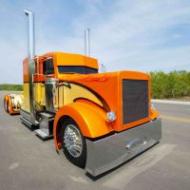
Быстрая переналадка оборудования. Общая структура проведения программы SMED Быстрая переналадка с помощью 5s
Мне нравится
6Определение
SMED/Быстрая переналадка (Single-Minute Exchange of Die - англ. одноминутная замена штампов) - это концепция организации процесса переналадки/переоснастки оборудования, позволяющая значительно сократить затраты времени при переналадке оборудования.
Концепция зародилась в Японии в 1950 г. на машиностроительных заводах, автором концепции является Сигео Синго, который разрабатывал данную концепцию в течение 20 лет (1950 -1970 гг.). Предполагая, что любую переналадку можно осуществить в течение 10 минут, он назвал свою концепцию SMED.
Дальныйшее совершествование SMED привело к появлению концепции OTED (One-Touch Exchange of Die - англ. замена штампов в одно касание) - концепция замены штампов не дольше одной минуты.
Методы SMED/OTED
В основе методов SMED/OTED лежит открытое в 50-х годах XX в. Сигео Синго разделение процесса переналадки на два типа операций:
Внутренние операции переналадки (IED - Internal Exchange of Die) - операции, которые можно выполнить только на остановленном станке, такие как монтаж или удаление штампа.
Внешние операции переналадки (OED - Outernal Exchange of Die) - операции, которые можно выполнить, когда станок еще работает, такие, как транспортировка штампа к месту хранения и от него.
Выделяют 8 основных методов системы SMED, используемых для снижения времени переналадки:
1. Разделение внутренних и внешний операций переналадки
Необходимо четко определить, какие операции переналадки должны выполняться при остановленном станке, а какие могут выполняться при работающем станке.
2. Преобразование внутренних действий во внешние
Преобразование требует пересмотра операций с целью проверки не осталось ли среди действий отнесенных к внутренней переналадке, тех которые на самом деле являются или могут являться внешними.
3. Стандартизация функций, а не формы
Стандартизация формы штампов требует больших затрат, в то время как стандартизация функций требует только однородности деталей, необходимых для операции переналадки. Например, добавление пластины или блока к краю приспособления штампа стандартизирует размеры только этой детали и делает возможным применение одних и тех же зажимных устройство при различных наладках.
4. Применение функциональных зажимов или полное устранение крепежа
На практике наиболее часто используемое крепежное устройство - болт, но его применение порой требует очень большого времени. Например, болт с 15 витками резьбы, нужно повернуть 14 раз, прежде чем он будет действительно затянут на последнем обороте. Но нужен только последний оборот при затяжке и первый при ослаблении, остальные 13 - потерянные движения. Болты не единственный способ крепления, методы крепления в одно касание, использующие клинья, пальцы, и защелки или пружины как захватные приспособления, просто соединяющие две детали, снижают время установки до секунд.
5. Использование дополнительных приспособлений
Некоторые из задержек, связанные с регулировками при внутренней наладке, можно устранить путем использования стандартных приспособлений. Когда обрабатывается заготовка, закрепленная в одно приспособление, следующая заготовка устанавливается во второе приспособление. Когда обработка первой заготовки закончена, второе приспособление легко ставится на станок для обработки.
6. Применение параллельных операций
Если операция переналадки требует установочных операций со всех сторон станка, и если эти операции выполняет один рабочий, то много времени и сил затрачивается на хождение вокруг станка. Но когда параллельные операции выполняют два человека, время переналадки обычно снижается более чем вдвое благодаря экономиидвижений. Например, операция занимающая у одного рабочего 30 минут, у двоих займет всего 10 минут.
7. Устранение регулировок
Обычно регулировки и пробный пуск занимают 50-70% времени врутреннней наладки. Их устранение дает поразительную экономию времени. Устранение регулировки начинается с осознания того, что установка переключателей/регуляторов и регулировка две разные и самостоятельные функции. Регулировки можно ликвидировать если использовать прибор для точного поределения правильного положения конечного выключателя/регулятора. Тогда единственно необходимая операция это установка переключателя/регулятора. Безусловно, лучшая регулировка - отсутствие регулировки. Например, регулировку можно исключить полностью, когда число положений регулятора ограничено и неизменно.
8. Механизация
Механизацию следует рассматривать тогда, когда приложены все усилия по улучшению процесса переналадки всеми вышеописанными способами. Механизация существенна для замены крупных приспособлений и штампов, литейных и прессовых форм. Закрепление каких-либо деталей может производиться при использовании давления воздуха или масла. Однако, инвестиции в механизацию следует оценивать очень тщательно. При сокращении времени переналадки предыдущими способами с 2 часов до 3 минут, механизация скорее всего уменьшит это время не более чем, еще на минуту.
Стадии внедрения
SMED предусматривает прогрессивный подход к совершенствованию переналадки. При этом необходимо пройти 4 стадии:
Стадия 1
На этой первоначальной стадии не делаются различия между внутренними и внешними действиями. Много внешних действий таких, как поиск инструментов и подготовка штампа, выполняются при остановленном станке. Это вызывает ненужное удлинение переналадки.
Стадия 2
Это наиболее критичная стадия при внедрении SMED. Она предусматривает разделение операций внутренней и внешней наладки. Составьте контрольный листок, включив в него все узлы, условия выполнения операций и шаги, которые нужно выполнть при работающем станке. Затем проверьте функционирование всех узлов чтобы избежать задержек при внутренней наладке. Наконец, нужно исследовать и внедрить наиболее эффективный способ транспортировки штампов и других частей при работе станка.
Стадия 3
Проанализируйте текущий процесс переналадки, чтобы определить, можно ли какое-либо из внутренних действий преобразовать во внешние. Например, разогрев литейной формы, когда станок еще работает, устраняет необходимость разогрева формы во время остановки станка.
Стадия 4
Изучите операции внутренней и внешней наладки с целью выявления дополнительных возможностей для улучшений. Рассмотрите возможности исключения регулировок и изменения методов крепления.
За долгие годы из нескольких сотен усовершенствований SMED наиболее результативными оказались:
- четкое разделение внутренней и внешней переналадки
- по возможности полное преобразование внутренней наладки во внешнюю
- устранение регулировок
- осуществление крепления без винтов
Оказывается, любую переналадку можно сократить как минимум в два раза. Однако этот процесс связан с определенными трудностями. На конкретных примерах оценим методику сокращения продолжительности переналадки оборудования без потери качества производства.
Переналадка и быстрая переналадка — в чем разница
Предприятий, имеющих отдельное оборудование для каждого вида продукции, практически не осталось. Держать его невыгодно, особенно когда рыночная конкуренция заставляет постоянно расширять продуктовую линейку для максимального удовлетворения растущих и меняющихся потребностей клиентов. Переналаживаться приходится всем.
Время переналадки - это период времени между выходом последнего годного продукта А и получением первого годного продукта В. Другими словами, это время, в течение которого оборудование не производит продукт (ни А, ни В), а перестраивается и перенастраивается . С точки зрения философии бережливого производства это время является потерянным, так как в течение него не производится и не видоизменяется продукт, а значит, не создается никакой ценности. Для сокращения этой потери и был сформулирован метод SMED (single minute exchange of die - метод быстрой переналадки). SMED означает сиюминутную замену пресс-форм (штампов) или замену штампов за несколько минут. Суть метода - детальный анализ и поэтапное сокращение каждой составляющей переналадки . Метод можно применять гораздо шире - например, при замене инструмента, узлов машин, перестройке программного обеспечения, замене материалов, красок, комплектующих и т. д.
Итак, термин «быстрая переналадка» означает методику сокращения ее продолжительности.
Примеры в деталях
Цель, которую преследовали создатели метода в середине прошлого века, заключалась в необходимости сокращения размеров партий производства. Японские компании первыми поняли, что в современных условиях предприятие должно быть гибким и быстро реагировать на изменение спроса, а также что наиболее экономичными будут ритмичное производство и отгрузка небольшими партиями. Логика простая: меньше партия между переналадками - меньше запасов в производстве - быстрее исполняется заказ - больше заказов можно выполнить. Сокращение запасов в производстве благодаря работе меньшими партиями приводит к сокращению потерь, связанных с перекладыванием, сортировкой и отбраковкой запасов. Японцы старались сократить продолжительность переналадок оборудования, чтобы чаще их осуществлять и работать как можно меньшими партиями .
Если раньше на переналадку тратили 60 мин. в день и сократили ее продолжительность до 30 мин., то использовать освободившиеся 30 мин. можно по-разному. Самое простое решение - производить продукцию больше и дольше на 30 мин. Японские компании искали такое решение, чтобы переналаживать оборудование в два раза чаще . Теперь вместо одной переналадки продолжительностью 60 мин. можно выполнить две переналадки по 30 мин. Значит, можно сократить размер партии между переналадками в два раза. Если через производственные операции партия проходит в два раза меньше, следовательно, и продукт пройдет через производство в два раза быстрее, и незавершенного производства на рабочих местах будет в два раза меньше. Разумеется, существует множество других факторов, влияющих на скорость и количество незавершенного производства. На данном примере видна прямая зависимость между продолжительностью переналадки и временем исполнения заказа.
Словосочетание «частая переналадка» не укладывается в голове среднестатистического российского руководителя, особенно старой закалки. Многолетние управленческие парадигмы сводятся к тому, что переналадка - это плохо, чем реже она происходит, тем эффективнее работа, так как оборудование меньше простаивает . Последняя парадигма полностью противоречит философии бережливого производства. Чем реже происходит переналадка, тем больше партии в производстве и запасы на складе. А излишние запасы - это один из видов потерь с точки зрения бережливого производства, они порождают ненужную работу . Их необходимо укладывать, транспортировать, сортировать, считать, переставлять, отбраковывать. Существует зависимость: чем больше запасов продукции или незавершенного производства, тем больше в нем бракованной продукции. Продукт трется друг об друга, падает, ударяется, ржавеет, пылится во время хранения и манипуляций с ним. Кроме того, дефекту всегда проще затеряться в большой массе продукции. «Идеальный» вариант работы любого производственного руководителя - изготовление одного вида продукции месяцами без переналадки. Это удобно только руководителю и наладчику, а организация из-за такой работы будет нести затраты.
Стоит отметить, что частые переналадки и работа меньшими партиями требуют не только сокращения продолжительности переналадок, но и обеспечения ритмичной передачи партий на следующие операции.
Например, мы можем сократить продолжительность переналадки с 60 мин. до 30 мин., но в этом не будет практического смысла, если не увеличить частоту отгрузок, т. е. мы не будем поставлять уменьшенные партии на следующую операцию в два раза чаще. Или, например, будем ждать, пока наполнится большая тара (коробка, палета и т. д.), чтобы ее перевезти. Такая дополнительная работа противоречит старым и привычным парадигмам.
«Мало того что нужно сократить время переналадки, так еще и передачу партий менять… Это слишком сложно, лучше произведем больше за это время» - примерно так рассуждает среднестатистический руководитель.
Применяя быструю переналадку, большинство предприятий имеют хорошие результаты в виде сокращения ее продолжительности, однако эти показатели применяются ограниченно. Высвобождаемое время используется для уменьшения сверхурочных работ, производства большего количества продукции, выполнения планового ремонта и обслуживания и т. д. Сократить время переналадки, чтобы чаще переналаживаться, удается не всем. Для этого требуется изменение мышления и принятие новых управленческих парадигм.
Поверхностное применение
Данная особенность заключается в том, что в большинстве случаев предприятия не используют потенциал метода на 100%. Почему же так происходит?
В таблице приведена информация о четырех переналадках оборудования для демонстрации того, почему метод применяется поверхностно .
Продолжительность до начала работ - время переналадки, на которое ориентировались до того, как начали его оптимизировать и, соответственно, измерять. Другими словами, это примерное время, которое фиксировалось на основании ощущений наладчиков и линейных руководителей.
Измеренная продолжительность - реальная продолжительность переналадки, которая фактически измерена секундомером рабочей группой на месте. Метод предполагает анализ наиболее продолжительных переналадок с выполнением нескольких замеров времени.
Продолжительность после оптимизации - время переналадки после анализа и выполнения разработанных мер.
Все меры, принятые в ходе сокращения продолжительности переналадок, объединены в три направления улучшений.
Попустительство.
Это время, на которое закрывают глаза; запас времени на спокойствие руководителя, дающий уверенность в том, что даже при возникновении проблем переналадка будет выполнена в срок. Фактически это разность продолжительности до начала работ и измеренной продолжительности переналадки.
Например, раньше считалось, что переналаживаться нужно час, а когда посмотрели на переналадку, поняли, что это занимает не больше 45 мин. С одной стороны, разница небольшая, и 45 мин. округляли до одного часа. С другой, бережливой стороны, 45 мин. - это на четверть меньше часа. Если в день 12 переналадок, то путем округления мы теряем не 15 мин., а 180 мин., или три часа рабочего времени. А три часа рабочего времени при двух сменах работы и 22 рабочих днях - это уже 132 часа, или 16,5 рабочей смены (по восемь часов), или более восьми рабочих дней (по две рабочие смены). Можно не обратить внимания на 15 мин., но невозможно закрыть глаза на 16,5 рабочей смены.
Такие потери времени выявляются на стадии наблюдения, они присутствуют в любой переналадке, которую никогда не оптимизировали. Средний процент попустительства составляет 24,1% (от 3,1 до 37,8%). Это означает, что почти четверть времени при проведении переналадки можно высвободить, просто понаблюдав за ней и устранив явные потери.
Организационные решения
- решения, связанные с изменением последовательности работ, предварительной подготовкой и рационализацией порядка переналадки. В большинстве переналадок скрыт большой потенциал, относящийся к предварительной подготовке. Собственно, метод и основан на принципе разделения внутренних и внешних действий при переналадке, т. е. тех, которые можно выполнить только при остановленном оборудовании, и тех, которые можно выполнить до остановки или после запуска. Организационные решения обязательно предполагают закрепление в виде стандарта (подготовки, переналадки, хранения инструмента и т. п.). Кроме того, они предусматривают обеспечение обязательного контроля над соблюдением стандарта. Выполнять работу по-новому означает формировать новые привычки. Формировать новые привычки никто не хочет, поэтому необходим пристальный контроль руководителя. Организационные решения в примерах занимают 30,7% (от 6,1 до 49%). Они не требуют больших материальных затрат, однако нужно время для закрепления новых привычек у работников.
Технические решения.
Речь идет об изменении конструкции оборудования и оснастки - изменении крепежей, применении быстросъемных элементов и т. д. Подобные решения разрабатываются индивидуально для конкретной переналадки. На практике это происходит в виде мозгового штурма, который проводится с группой заинтересованных лиц. Количество и качество решений зависит только от того, насколько руководство предприятия готово к изменениям и проявлению творческих способностей. Это самое тяжелое направление работ.
Ограничивающие парадигмы, которые встречаются практически всегда, заключаются в том, что люди считают невозможным внесение каких-либо изменений в оснастку и оборудование.
Именно поэтому возможности применения быстрой переналадки существенно ограничены. Разумеется, можно устранить явные потери и рационально организовать работу наладчиков: подготовить заранее оснастку и инструмент, организовать рабочие места и создать все условия для работы. Часто этого бывает достаточно, но важно понимать, что организационные мероприятия требуют постоянного контроля и выработки привычек. Нужны стандарт и постоянная проверка его соблюдения. От попустительства никто не застрахован. Всегда существует вероятность того, что улучшения из первых двух столбцов вернутся в первоначальное состояние (см. таблицу). С другой стороны, технические изменения - это изменения раз и навсегда. Упростите крепеж, избавьтесь от старого - и наладчику некуда будет деваться. Он будет вынужден выполнять переналадку по-новому. В примерах доля экономии времени за счет технических решений составляет 15,1% (от 8,2 до 24%), что существенно меньше, чем в предыдущих двух направлениях.
Это не означает, что отсутствует техническая возможность для совершенствования. Ограничения мы ставим сами. Просто руководство предприятий не было готово к большим изменениям. Возможно, в тот момент изменения не были столь нужны, чтобы углубляться в процесс переналадки и оптимизировать его.
В последнем столбце таблицы приводится потенциал дальнейшего сокращения продолжительности переналадок, который отражает ситуацию, близкую к идеальной, при максимальном применении технических решений. Многие переналадки можно было бы уменьшить не наполовину, а на 80-90%.
Бережливое производство (Lean) — одна из «долгоиграющих» концепций управления отдельными проектами и предприятиями. Её основы были заложены в первой половине XX ст. крупнейшим автомобильным предприятием того времени — Toyota. А SMED один из инструментов такого подхода к проектному менеджменту.
В рамках lean-production функционирует десяток методов и инструментов , которые в комплексе с позволяют достичь высокой эффективности рабочего процесса.
Бережливое производство в той или иной форме используется в международных (Oriflame Cosmetics, Toyota) и национальных (украинские «УПЭК», «ТБМ») компаниях.
История бережливого производства
Противостояние — вот настоящий двигатель прогресса. Благодаря негласной борьбе между двумя автогигантами, Ford и Toyota, были заложены основы lean production.
В 1913 году Генри Форд создал первую в мире модель производственного потока. Обрабатываемое изделие передвигалось по конвейеру от одного рабочего процесса к другому, и в итоге превращалось в Ford Model T , вошедший в десятку автомобилей, изменивших мир по версии журнала Forbes. Использование автоматизации снизило себестоимость машины и позволило обеспечить серийный миллионный выпуск.
Тем не менее, у модели организации производства Форда было ровно два недостатка:
- отсутствие разнообразия продукции — заводы были заточены на выпуск одной модели в одном цветовом решении и спецификации.
- ограниченность пропускной способности — серийное производство требовало непрерывного выпуска изделий, и чем сильнее росли объемы, тем больше становились задержки между отправкой изделия на следующий рабочий процесс.
Спустя 26 лет после выпуска Model T в продажу, в Японии провели перепрофилирование Toyota.Вместо текстиля концерн стал выпускать автомобили. Основатель Toyota Motor Corp, Киширо Тойдода главным в борьбе за качество определил детальное изучение каждой стадии производственного процесса . Отчасти благодаря этому компании удалось выиграть первый тендер в 1936 г. на производство грузовиков.
Развить идею до крепкой концепции помешала Вторая мировая война. Toyota нуждалась в кардинально новом решении , так как послевоенная экономика Японии пребывала в катастрофическом положении. Около 40% национальных промышленных заводов и инфраструктуры были разрушены, и уровень производства упал до значений начала 30-ых гг.
Тайити Оно, ставший директором Toyota в 1950 г., решил позаимствовать опыт США. В штатах он и познакомился с одним из чудес «американской мечты» — супермаркетами, в которых запасы пополнялись по мере необходимости. Посетил директор и заводы Генри Форда. По возвращению на родину Тайити Оно вместе с Сигео Синго решили поставить во главу угла стратегию (производство согласно реальному спросу) , а не выталкивания (производство — на планируемых объемах продаж).
Комплекс методов реализации стратегии получил название Toyota Production System — TPS, и стал прообразом Production. Само понятие «бережливое производство» ввела в обиход Машина, которая изменила мир Дж. Вумека и Д. Джонса .
Методы бережливого производства
SMED, о котором пойдёт речь сегодня, важный, но не единственный инструмент воплощения бережливого производства.
В концепции Lean Manufactoring выделяют такие методы:
- поток единичных изделий (single-peace flow) — за одну единицу времени производится и перемещается только одно изделие. Среди явных преимуществ — устранение проблемы многозадачности, выравнивание нагрузки на мощности и гибкость производства.
- — система-реализация принципа «точно в срок». К плюсам относятся: прозрачность и понятность процесса разработки для команды проекта, стимулирование инициативы каждого работника, выполнение задач в срок.
- — концепция управления и обслуживания производственного оборудования. Без этого метода невозможно представить бережливое производство.
- Система 5S — система организации рабочего места. Согласно А. Пырьеву комфортным является минимум в 9 квадратных метров рабочего пространства на одного человека. По его же исследованиям, использование офисов с открытой планировкой (персональные рабочие столы на большом пространстве) наименее эффективно с точки зрения удовлетворённости работников и производительности труда.
- быстрая переналадка (SMED) — от английского «Single Minute Exchange of Dies » — «быстрая замена штампов». Позволяет быстрее переключаться между стадиями производственного процесса, а значит уменьшать финансовые и временные затраты на создание и хранение продукции.
- — философия, которая фокусируется на непрерывном совершенствовании процессов производства, разработки, вспомогательных бизнес-процессов и управления. В основе — 5 элементов: аккуратность, порядок, чистота, стандартизирование, дисциплина.
- («защита от ошибок») — или «бака-ёкэ» («защита от дурака»). Подразумевает защиту техники, инструментов, изделий на разных этапах процесса, ПО и т.п. от очевидно неверных действий человека при взаимодействии с этими предметами.
Пожалуй, вся упаковка техники в современности изготавливается по принципу пока-ёкэ. Под каждый элемент есть конкретный слот, и ошибиться в размещении невозможно.
Создание SMED
Как и концепция бережливого производства, SMED стала результатом коллаборации исследователей и производителей на протяжении XX века.
Эта статья познакомит Вас с возможностями сокращения времени на переналадку и техническое обслуживание оборудования. В статье пойдет речь о системе, известной под аббревиатурой SMED (от англ. Single Minute Exchange of Dies, быстрая замена штампов). Эта система по своей сути считается набором теоретических и практических инструментов, с помощью которых можно значительно сократить время операций наладки и переналадки оборудования. Сегодня в условиях жесткой конкуренции и постоянного реагирования на последствия мирового экономического кризиса, скорость переналадки является одним из ключевых показателей, характеризующих эффективность работы предприятия. Возможности быстрой переналадки позволяют быстро менять модельный ряд и избегать скапливания лишних запасов продукции на складе. Один из первых опытов внедрения системы SMED в производственный процесс компании Toyota доказал, что использование этой системы позволяет снизить время переналадки большого 1000-тонного пресса с четырех часов до трех минут.
С первого взгляда может показаться, что не все элементы этой статьи могут быть применимы для отраслей промышленности, эксплуатирующих чистые помещения. Однако сегодня система SMED используется повсюду - от механообрабатывающих цехов и упаковочных линий, до авиакомпаний и инжиниринговых центров.
Статья будут полезна всем нашим читателям и тем, кто хочет овладевать новыми компетенциями. Процесс улучшений возможен лишь при вовлечении всех работников и их всестороннем обучении методам и инструментам бережливого производства.
Быстрая переналадка оборудования
А.В. Александров, главный редактор, президент Группы компаний ВИАЛЕК
Производственный процесс – это некая последовательность действий по превращению сырья в готовые изделия. Проще говоря, процесс – это то, как что-то делается. Производственные процессы разделяются на пять основных стадий:
- Подготовка;
- Обработка;
- Контроль;
- Транспортировка;
- Хранение.
Подготовка включает в себя очистку, демонтаж и сборку. Обработка обеспечивает изменение формы или свойств материалов. Контроль подразумевает сравнение со стандартом. Транспортировка – это перемещение продукции. Соответственно, хранение – это период, в течение которого обработка, транспортировка или контроль продукции не происходят. Каждая стадия производственного процесса состоит из операций по переналадке, т.е. операций по подготовке или регулировке оборудования, которые выполняются до и после обработки каждой партии изделия.
Многие компании производят свою продукцию большими партиями только потому, что длительность процесса переналадки делает процесс замены продукции на линии очень дорогостоящим. Потери, связанные с простоем оборудования, иногда исчисляются миллионами рублей. В то же время изготовление продукции крупными партиями также имеет несколько недостатков:
- Задержки;
- Потери, связанные с запасами продукции;
- Ухудшение качества.
Заказчикам приходится дожидаться, пока предприятие изготовит всю партию продукта (изделия), хотя достаточно было бы произвести и меньшее количество. Последующее хранение нереализованной продукции порождает дополнительные затраты, требует привлечения других ресурсов предприятия и увеличивает вероятность того, что эту продукцию придется направить в переработку или даже на уничтожение в связи с порчей. Естественно, все это не добавляет ценности продукту (изделию).
Система SMED (Single Minute Exchange of Dies - быстрая замена штампов) позволяет отказаться от предубеждения, что переналадка требует значительного времени. Если процесс переналадки занимает очень мало времени, ее можно проводить так часто, как это требуется. Это в свою очередь означает, что если мы будем производить продукцию малыми партиями, то сможем получить много преимуществ:
- Гибкость;
- Быстрая поставка;
- Производительность;
- Высокое качество.
Предприятие может удовлетворить меняющиеся потребности заказчиков без издержек на хранение запасов продукции. Производство малыми партиями позволит сократить время, затрачиваемое на подготовку заказа к отправке, а также время ожидания заказчиком требуемой продукции. Соответственно, снижается вероятность порчи изделий, поскольку сокращается время их хранения. Уменьшается и объем производственного брака из-за меньшего числа ошибок в ходе наладки и пробных пусков оборудования.
Первоисточником для этой статьи является фундаментальная монография Сигео Синго (Shigeo Shingo) «Быстрая переналадка: революционная технология оптимизации производства». Создатель системы SMED, Сигео Синго, в течение почти 20 лет, посещая производства и наблюдая, что и как рабочие делают во время переналадки оборудования, однажды осознал, что все необходимые действия можно и нужно производить наикратчайшим образом. Основная идея автора этой системы заключается в том, что нужно отойти от «шаблонного» подхода к переналадке, взглянуть на этот процесс с другой стороны и найти нужное и более эффективное решение. Система SMED является довольно простым и универсальным решением, которое успешно используется по всему миру. Логика SMED основана на двух ключевых принципах:
- Разделение операций по переналадке на внутренние и внешние действия;
- Преобразование как можно большего числа внутренних действий переналадки во внешние позволяет в несколько раз сократить время переналадки.
Внутренние действия по переналадке – это операции, которые выполняются только после остановки и/или выключения оборудования. Например, пресс-форму или систему фильтрации можно заменить только при остановке единицы оборудования. Внешние действия по переналадке – это операции, которые можно выполнять во время работы оборудования. Например, болты крепления пресс-формы для следующего изделия можно отобрать и отсортировать еще при работающем станке, так же как и собрать и проверить систему фильтрации для следующего продукта.
Традиционная переналадка
Независимо от типа используемого оборудования, все процедуры традиционной переналадки (т.е. без использования системы SMED), состоят из четырех этапов:
- Подготовка, регулировка, проверка материалов и инструментов;
- Монтаж и демонтаж съемных элементов;
- Измерения, настройка и калибровка;
- Пробные пуски и калибровка.
На первом этапе, при подготовке, регулировке и проверке инструментов проверяется наличие, правильное местоположение и работоспособность всех деталей, съемных частей и инструментов. В системе традиционной переналадки все подготовительные действия выполняются уже после остановки оборудования.
На втором этапе традиционной переналадки с оборудования снимаются съемные элементы, детали, производится их очистка и т.п. На данном этапе также может производиться установка новых инструментов для обработки следующей партии изделий. Эти действия выполняются после того, как завершена обработка партии изделий. Как правило, такие действия выполняются при отключенном оборудовании и относятся к операциям внутренней наладки. Из таблицы 1 видно, что этот этап, т.е. непосредственно переналадка, занимает по сравнению с другими этапами гораздо меньше времени.
Третий этап, измерения, настройка и калибровка, включает все работы по измерению и калибровке для обеспечения производства, например, центровка, задание размеров, температуры, давления и т.п. В большинстве случаев для проведения таких работ также требуется остановка оборудования.
И последний, четвертый этап – пробные пуски и регулировка, – подразумевает работы по корректировке, выполнению пуска оборудования и производства пробной единицы изделий. Получается, что чем точнее и аккуратнее были произведены измерения и калибровка на предыдущем этапе, тем проще провести регулировку оборудования на этом этапе. Соответственно, при традиционной переналадке время, затрачиваемое на пробные пуски и регулировку оборудования, зависит от квалификации и опыта рабочего. Как показано в таблице 1, на этот этап тратится около 50 % всего времени переналадки. При традиционной переналадке оборудование производит некачественную продукцию до тех пор, пока не завершится данный этап. Поэтому регулировка и пробные пуски относятся к операциям внутренней наладки.
Основная причина, из-за которой традиционные операции переналадки занимают много времени, заключается в том, что операции внутренней и внешней наладки перемешаны между собой. Многие задачи, выполнить которые можно и при работающем оборудовании, выполняются только после его остановки.
Таблица 1 – Базовые этапы наладки и время их выполнения до внедрения системы SMED
№№ |
Этапы наладки |
Доля времени конкретной операции в процессе наладки до внедрения системы SMED |
Подготовка, проверка материалов и инструментов | ||
Демонтаж и монтаж съемных частей, инструментов | ||
Измерения, настройка и калибровка | ||
Пробные пуски, регулировка | ||
Источник : «Quick Changeover for Operators. The SMED System» by Shigeo Shingo, 2000 |
Возможности системы SMED
В то же время система SMED призвана упростить и сократить действия при переналадке. Например, она позволяет сократить время операций на третьем этапе традиционной переналадки, предлагая производить все или большинство подготовительных операций при работающем оборудовании, а также обеспечить изготовление качественной продукции сразу же после запуска без пробных запусков и регулировки, другими словами полностью отказаться от четвертого этапа традиционной переналадки.
Система SMED внедряется в четыре этапа: один подготовительный и три основных (рис. А). Подготовительный этап, так называемый анализ процесса наладки, помогает разобраться в том, как именно выполняются процессы наладки каждой конкретной единицы оборудования. Этап 1 – разграничение операции внешней и внутренней наладки. Только благодаря первому этапу можно сократить простои оборудования, происходящие в процессе переналадки, на 30-50%. Этап 2 – трансформировать некоторые операции внутренней наладки в категорию внешних. Второй этап позволяет еще больше сократить время переналадки. И последний, третий этап направлен на оптимизацию всех действий по переналадке.
Анализ процесса переналадки
Анализ процесса переналадки является подготовительным этапом для системы SMED и состоит из трех основных шагов. Прежде всего, необходимо провести видеосъемку для фиксации на видеокамеру всех действий по переналадке. При этом необходимо обращать внимание на движение рук, глаз и любые перемещения работника, выполняющего переналадку оборудования. Поэтому желательно использовать функцию видеокамеры по фиксации даты и времени съемки. Второй шаг направлен на подробное изучение видеозаписи с помощью функций «Пауза» и «Перемотка». На этой стадии необходимо обратить внимание на последовательность движений и время, которое на них затрачивается для каждого этапа переналадки. Поэтому, возможно потребуется использование секундомера. И третий, подготовительный шаг анализа процесса переналадки заключается во всестороннем обсуждении отснятого видеоматериала с работниками (операторами, наладчиками, мастерами), которые тем или иным образом участвуют в переналадке соответствующего оборудования. На этой стадии необходимо тщательно задокументировать все расхождения между словами работников и действиями, зафиксированными с помощью видеокамеры.
Этап 1. Разделение внутренних и внешних действий по переналадке
Первый этап является наиболее важным этапом при внедрении системы SMED. На этом этапе процесс переналадки разделяется на внутренние и внешние операции. Т.е. осуществляется четкое разграничение действий на те, которые можно выполнить при работающем оборудовании (например, транспортировка и подготовка инструментов), и на те, которые должны выполняться только после его остановки.
Логика этого этапа заключается в том, что отдельные задачи можно с легкостью выполнить до того, как оборудование будет остановлено на переналадку. В число таких задач входят поиск и назначение конкретных исполнителей, подготовка необходимых деталей и инструментов, некоторые ремонтные работы, транспортировка деталей и инструментов к оборудованию. Но, что удивительно, на практике эти задачи очень часто выполняются лишь после остановки оборудования, хотя их вполне можно реализовать в то время, когда обрабатывается предыдущая партия изделия. Выделив эти задачи в процесс внешней наладки, можно сократить время переналадки, т.е. простоя оборудования, на 30-50%. Разделить операционные задачи на внутренние и внешние помогают три практических метода – контрольные листы, функциональные проверки и оптимизация процесса транспортировки.
В контрольных листах перечисляются действия и другая информация, необходимая для подготовки и запуска последующих операций. Используя контрольные листы, можно убедиться, что все инструменты, съемные элементы (детали), работники и документация находятся именно там, где они и должны быть. Тем самым контрольные листы позволяют избежать различных погрешностей и ошибочных действий, а соответственно и повторных запусков оборудования.
Следующий метод – функциональная проверка – позволяет убедиться в том, что все инструменты, съемные элементы и детали находятся в исправном состоянии. Если своевременно не провести функциональную проверку, то выявление брака на последующих этапах может привести к длительной задержке операций внутренней переналадки. Функциональные проверки дают возможность произвести необходимый ремонт или замену деталей до начала переналадки. И наконец, можно еще больше сократить время, затрачиваемое на операции внутренней переналадки. Для этого необходимо оценить возможности оптимизации операций по транспортированию деталей и инструментов. Во время наладки или технического обслуживания все съемные элементы, инструмент и средства измерений часто транспортируются из зоны хранения к оборудованию и, соответственно, обратно после окончания процесса. Чтобы сократить время простоя оборудования, необходимо производить все действия по транспортировке как операцию внешней наладки. Другими словами, новые детали и инструменты необходимо доставлять к оборудованию еще до его остановки на переналадку, а снятые с оборудования детали и инструменты транспортировать на склад уже после установки новых форматных частей и запуска оборудования.
Первый этап позволяет уменьшить время переналадки, но сам по себе не может сократить его существенно. Поэтому нужен следующий этап, предлагающий преобразование как можно большего числа внутренних операций наладки во внешние.
Этап 2. Преобразование внутренних действий по переналадке во внешние действия
На этом этапе «быстрой переналадки» необходимо преобразовать как можно больше внутренних действий по переналадке во внешние действия, т.е. осуществляемые при работающем оборудовании. Внедрение этого этапа происходит в два шага: 1) определение реальных функций и целей каждой операции, совершаемой в процессе внутренней переналадки, и 2) поиск путей для того, чтобы преобразовать часть этих (внутренних) операций во внешнюю наладку.
Успешно реализовать второй этап системы SMED невозможно без критического анализа принятой на предприятии практики внутренней переналадки. Чтобы успешно пройти второй этап быстрой переналадки, необходимо критично, как бы со стороны, оценивать свои действия. На этом этапе важно не позволять старым привычкам и убеждениям мешать процессу оптимизации производства.
Преобразовать внутренние действия по переналадке во внешние помогут три практических метода: 1) предварительная подготовка рабочих условий; 2) стандартизация наиболее важных функций и 3) использование специализированной вспомогательной оснастки.
Под предварительной подготовкой рабочих условий подразумеваются действия по сбору, компоновке и приготовлению необходимых деталей, инструментов и условий, произведенные до начала операции внутренней наладки. Предварительная подготовка предполагает, что все действия по приготовлению деталей, инструментов и другого оборудования тщательно спланированы еще до остановки оборудования на переналадку.
Рассмотрим, например, ситуацию, когда мы имеем дело с проволочной или тканой заготовкой, поставляемой в тяжелых катушках. Новые катушки приходится транспортировать к оборудованию с помощью вилочного погрузчика, но, к сожалению, погрузчик не всегда «под рукой». Избежать простоев оборудования, вызванных поиском погрузчика, позволит использование специальной конструкции-держателя для дополнительной катушки. В эту конструкцию размещается дополнительная катушка, и когда проволока (или ткань и т.п.) на катушке заканчивается, оператор останавливает станок, снимает пустую катушку, и достаточно легко и быстро перемещает новую катушку на рабочий вал оборудования.
Следующий инструмент внедрения системы SMED – стандартизация функций - позволяет выделить те детали и их функции, которые являются наиболее важными в процессе переналадки. Важно пристально рассмотреть каждую функцию и определить, можно ли какую-то из них стандартизировать. Также необходимо подумать, как эти функции упростить, свести к замене лишь небольшого числа деталей или съемных частей. Ведь самый простой и быстрый способ замены чего-либо – это не заменять вообще ничего или заменять самый минимум. Например, если для новой операции необходимы инструменты и детали, отличные от применявшихся для предыдущей операции, рабочие вынуждены в ходе переналадки очень часто останавливать оборудование и производить различные регулировки, которые требуют больших затрат времени. Стандартизация помогает избежать подобных внутренних операций наладки, так как она позволяет использовать одни и те же детали и конструкции для различных операций – задание размеров, центровка, закрепление, съем и затяжка деталей и инструментов. На этом этапе рекомендуется разработать маршрутную карту для каждой операции переналадки. В технологической карте отмечаются последовательность шагов, которые должен выполнить наладчик, время, затрачиваемое на этот шаг, а также способ подачи сигналов другим участникам переналадки (если это необходимо). Четкое следование по маршрутной карте гарантирует, что каждый участник переналадки, знает, что именно и когда ему делать.
Третий инструмент - использование вспомогательной оснастки - позволяет без значительных затрат преобразовать внутренние действия по переналадке во внешние. Вспомогательная оснастка – это плиты или рамы, имеющие стандартный размер, из-за чего можно легко заменять их на оборудовании. Такой подход эффективен, когда рабочая оснастка или съемные элементы для изготовления разных изделий имеют разные размеры, и соответственно, в условиях традиционной переналадки их замена, закрепление и центрирование потребует остановки оборудования. Использование вспомогательной оснастки предполагает изготовление двух стандартных технологических плит, на которые в зависимости от типа операции будут устанавливаться детали, инструменты разных размеров. Все действия по закреплению и регулировке (центровке, установке отступов и т.п.) проводятся непосредственно на этих плитах в то время, пока обрабатывается предыдущая партия изделия. Закончив работать с одной оснасткой, ее вынимают и просто вставляют другую, минуя операции центровки и крепления на оборудовании. Поскольку вспомогательные оснастки стандартизированы, непосредственно установка сводится к фиксированию оснастки в отведенном для нее месте на оборудовании.
Этап 3. Оптимизация действий
На последнем этапе внедрения концепции «быстрой переналадки» необходимо оптимизировать все действия по переналадке - как внутренние, так и внешние. Для этого следует еще раз тщательно пересмотреть все операции, их функции и цели. И практически во всех случаях именно этот этап является ключевым в достижении того, чтобы операции переналадки не занимали много времени. Практические инструменты, применяемые на этом этапе системы SMED, предназначены отдельно для внутренних и внешних действий по переналадке.
Для внешней переналадки используются способы сокращения длительности операций транспортировки и хранения деталей и инструментов. Как правило, для этого рекомендуют ответить на следующие вопросы:
- Как лучше всего расположить инструменты в месте хранения?
- Каким образом обеспечить работы по техническому обслуживанию и поддержанию инструментов в рабочем состоянии?
- Сколько именно и какие инструменты должны быть в наличии?
Например, если организовать места постоянного хранения съемных частей, инструмента и деталей в наиболее близких и удобных местах, это улучшит операции транспортирования и хранения. Дополнительная маркировка мест хранения и объектов, которые там размещаются, с помощью цветных кодов и номеров, указывающих их расположение в конкретном месте (помещение, шкаф или стеллаж в складской зоне) не только упрощает поиск нужных объектов, но и их последующее возвращение на места постоянного хранения.
Для оптимизации внутренних действий по переналадке предлагается четыре инструмента: внедрение параллельных операций, использование функциональных зажимов, отказ от регулировок и механизация.
Первый инструмент позволяет использовать параллельные операции, то есть разделить функциональные обязанности по переналадке оборудования между двумя или более наладчиками. Часто наладчику приходится выполнять некоторые операции в передней части производственной линии, а другие операции – в задней части. Когда один человек выполняет переналадку сложной линии, ему приходится постоянно «курсировать» от одного конца линии к другому, а это потерянное время и лишние телодвижения. Когда в подобной ситуации участвуют два (и более) работника, ее можно выполнить, скажем, не за 30 минут, а всего за 5, и это достигается только благодаря отказу от лишних и затратных по времени передвижений. Еще одним важным преимуществом такого подхода является повышение безопасности операций переналадки.
Второй метод – использовать функциональные зажимы, которые позволяют закреплять детали и инструменты с минимумом усилий и очень быстро. В операциях традиционной переналадки, для того чтобы закрепить на оборудовании съемные элементы или какие-либо детали, очень часто используются обычные болты. При этом болты теряются, или на поиск соответствующих друг другу болтов и гаек тратится много времени и усилий, не говоря уже о том, что часто болты приходится долго затягивать – все это увеличивает время переналадки. Чтобы избежать подобной траты времени система SMED предлагает перейти на использование функциональных зажимов – это крепежная деталь, которая позволяет зафиксировать объект в необходимом месте с минимальными усилиями и очень быстро. К таким функциональным зажимам относятся одноповоротные фиксаторы, фиксаторы «одним движением» и замковые фиксаторы.
Третий инструмент призван вообще ликвидировать операции пробных пусков и последующей регулировки оборудования, на которые тратится обычно до половины всего времени внутренней переналадки (см. Таблицу 1). Соответственно, если отказаться от корректировок (именно отказаться, а не сократить), то время простоя оборудования существенно сократится. Полный отказ от пробных запусков и корректировок достигается качественным выставлением установочных параметров оборудования еще до его запуска. Число пробных запусков и корректировок, которые нужно будет произвести, зависит от того, как точно (или наоборот, не точно) были выполнены работы по центровке, установлению размеров и режимов работы на предыдущих этапах наладки. Таким образом, чтобы ликвидировать регулировку, необходимо:
- использовать числовые установочные параметры;
- нанести четкие и хорошо заметные центровочные линии и
- применять систему LCM (от англ. Lost Common Multiple, наименьшее общее кратное).
Отказ от регулировки оборудования требует, чтобы наладчики, осуществляя наладку оборудования, полагались не на интуицию, а на четкие, фиксированные числовые установочные параметры. Один вариант – это создать градуированную шкалу, где отмечаются различные установочные параметры. Другой вариант – это применение калибров заданных размеров, которые позволяю устанавливать одинаковые расстояния между деталями. Следующий шаг – нанесение на оборудование центровых и дополнительных (плановых) линий обеспечивает правильность установки съемных элементов с первого раза и соответственно исключает характерный для традиционной переналадки метод «проб и ошибок».
Применение системы LCM, позволяет, не меняя некий съемный механизм, изменять его функцию. Многие операции, выполняемые на одном оборудовании, имеют схожие элементы, то есть выполняется что-то однотипное, но используются другие вырубные штампы, другие размеры, трафареты или функции. Система LCM сводит все эти однотипные элементы в единый механизм, и соответственно во время переналадки этот механизм не вынимается из станка и не заменяется, а переключаются только его функции – переустанавливаются параметры, поворачивается шпиндель с установленным на нем разным инструментом или просто переключается выключатель.
Четвертый и последний инструмент этапа оптимизации – механизация - применяется только после успешного внедрения предыдущих методов. Метод механизации нужно использовать для того, чтобы упростить и улучшить настройку оборудования, а не с целью значительного сокращения времени переналадки.
Заключение
Система SMED демонстрирует новый взгляд на процесс переналадки. Оперативная переналадка сокращает время простоя оборудования. Сокращение времени простоя оборудования делает работу более равномерной и спокойной. Более простой процесс наладки гарантирует бóльшую безопасность производства – меньше физических нагрузок или риска получения травм рабочими. Меньше запасов означает меньше суматохи на рабочем месте, что делает производственный процесс легче и безопаснее. Инструменты для наладки стандартизированы, поэтому следить нужно за меньшим числом инструментов. В результате – значительное увеличение производительности и снижение себестоимости изготавливаемой продукции.
В одном из последующих номеров журнала мы представим опыт специалистов Группы компаний ВИАЛЕК по применению методологии SMED для сокращения времени очистки многоцелевого фармацевтического оборудования при переходе с одного продукта на изготовление другого продукта.
4 617 специалистов посетили выставку с целью поиска товаров и услуг и получения актуальной отраслевой информации- Расширить географию сбыта
«Аналитика Экспо» - главное событие в области аналитической химии в России и странах СНГ.
Выставка является центральной бизнес-площадкой, объединяющей поставщиков аналитического
оборудования и специалистов различных научных и производственных лабораторий.
Посетители выставки «Аналитика Экспо» - это специалисты российских научных
и производственных лабораторий из различных отраслей промышленности: химической,
фармацевтической, пищевой, медицинской, нефтегазовой, строительной, экологической,
металлургической и других, а также научно-исследовательских организаций, здравоохранения
и государственных учреждений.
Ежегодно выставка показывает рост посетителей - в 2019 году 50% специалистов
присутствовали на выставке впервые.
Более 240 компаний
, ведущих отечественных и зарубежных производителей и поставщиков,
ежегодно принимают участие в выставке «Аналитика Экспо». Сейчас идет активный процесс
бронирования площади на 2020 год.
Успейте забронировать стенд на выставке «Аналитика Экспо 2020»!
Количество судебных споров, связанных с термолабильностью лекарств, увеличивается. Об этом в ходе круглого стола «Валидация процесса транспортировки лекарственных средств», организованным Советом профессионалов по цепям поставок, заявил руководитель практики «Здравоохранение» юридической фирмы «Пепеляев групп» Александр Панов.
Мероприятие состоялось в рамках третьей встречи рабочей группы «Фармацевтическая логистика» и собрало руководителей логистических компаний, а также представителей фармпроизводителей и дистрибьюторов.
Руководитель ГК «Виалек» Александр Александров, обратил внимание, что отклонения в температурном режиме далеко не всегда приводят к несоответствию продукта должному уровню качества. По его словам, перевозки без отклонений не бывает, о чем свидетельствует, в том числе, и зарубежный опыт.
«Невозможно обеспечить, чтобы температурный режим ни на минуту не вышел за пределы, - подчеркнул он. - Другой вопрос в том, что мы не должны допускать долгосрочных отклонений, и с юридической точки зрения это еще предстоит доработать, потому что сейчас в этом вопросе зачастую ставят знак равенства». Еще одна распространенная ошибка – мерить температуру воздуха, а не температуру продукта при перевозке, добавил он.
Продолжая тему неточностей в определениях, эксперт отметил, что за качество продукции отвечает производитель и держатель регистрационного удостоверения. И в этой связи не нужно манипулировать понятиями «эффективность и безопасность».
«Безопасность и эффективность подтверждаются на этапе доклинических и клинических исследований, - напомнил он. - Логисты обеспечивают это через применение надлежащих практик. Но говорить, что при перевозке нужно обеспечить безопасность и эффективность препарата, некорректно - перевозчики должны гарантировать, что транспортировка товара не оказала никакого влияния на качество продукта».
Подробности читайте в «ФВ» № 23 (978) от 23.07.2019 г. в публикации «Как повезет».
Возникновение SMED
Весной 1950 г. я проводил исследование на заводе Mazda Тoyo Kogyo в Хиросиме с целью повышения эффективности производства. Тогда там производились трехколесные автомобили. Фирма Toyo хотела расшить узкие места, образовавшиеся из-за прессов для штамповки крупных деталей кузова усилием 350, 750 и 800 т, которые работали с неполной нагрузкой. Я осмотрел производство и попросил начальника отдела, отвечающего за производство, разрешить мне провести хронометраж в течение недели, чтобы определить, как работают прессы. Он ответил, что это будет потерей времени: он уже знал, что именно прессы виновны в образовании узких мест, и поставил работать на них наиболее квалифицированных и сознательных рабочих. Три пресса работали круглые сутки, и он считал, что единственный способ увеличить производство — закупить дополнительное оборудование. Он очень надеялся, что высшее руководство именно так и поступит.
«Что же, плохо дело, — сказал я. — Но, может быть, мне все-таки можно провести такой анализ? Если выяснится, что другого способа ликвидировать узкие места нет, то я порекомендую руководству закупить дополнительное оборудование». После этого мне разрешили провести такое исследование.
На третий день производилась смена штампов на 800-тонном прессе. Рабочие сняли старый штамп и начали бегать вокруг пресса. Я спросил оператора, что происходит. Он сказал: «Пропал один из крепежных болтов нового штампа. Я был уверен, что он в штампе, но не могу его найти, хотя уже везде посмотрел».
— Когда вы найдете его, вы подойдете к прессу? Я буду вас здесь ждать, — сказал я.
— Хорошо, — сказал он. — Но все равно, когда вы здесь, я нервничаю.
Я сел возле пресса и стал ждать. Более чем через час оператор прибежал весь в поту, держа болт в руке, с радостным криком: «Вот он! Я нашел его! Фактически я не нашел его. Я просто взял длинный болт на соседнем прессе, обрезал его и нарезал резьбу. Поэтому и задержался. Можете поверить, это было непросто!» — сказал он.
Я посочувствовал ему, но тут же меня начала беспокоить другая мысль: Вы обрезали болт, взятый от другого пресса. А когда вам на том прессе нужно будет менять инструмент, что вы будете делать? У вас что, такое постоянно бывает?
— Да нет, не постоянно. Время от времени бывают такие казусы, — ответил он.
Именно тогда мне пришла мысль, что существует два фундаментально различных типа переналадки: внутренняя наладка — операции установки и снятия штампов, кото рые можно производить только на отключенном прессе; внешняя наладка — действия по транспортировке старых штампов на склад, доставке новых штампов к прессу; эти операции можно вы полнять без отключения пресса.
Подготовка болтов — внешняя операция. Не имело смысла останавливать работу 800-тонного пресса из-за отсутствия болта. Нужно было лишь четко отработать процедуры внешней переналадки, в том числе проверить наличие болтов для предстоящей переналадки.
Мы разработали тщательную процедуру подборки и хранения всех болтов в соответствующих коробках. Мы также улучшили процесс переналадки, выполняя все возможные операции как внешние. Это увеличило эффективность примерно на 50% и узкое место «рассосалось». После этого я взял за правило четко разграничивать внутренние и внешние операции.
Вот так «новорожденная» концепция SMED сделала свои первые шаги на Toyo Kogyo.
Второй эпизод
Летом 1957 г. меня попросили провести исследование на верфи Mitsubishi Heavy Industries в Хиросиме. Когда я спросил директора ремонтного завода г-на Мацудзо Окадзаки, в чем проблема, он сказал, что крупногабаритный строгальный станок для механической обработки деталей дизельных двигателей не используется на проектную мощность и желательно упростить эту операцию.
Проведя анализ производственного процесса, я обнаружил, что разметка под центровку и под размеры блока цилиндров двигателя производилась непосредственно на столе станка. Это в огромной степени снижало скорость работ. Когда я обсуждал это с г-ном Окадзаки, меня осенило: а почему бы не установить второй стол для строгального станка и не выполнять операцию разметки на нем отдельно? Таким образом мы смогли бы просто менять столы при переходе от одной партии к другой, и это значительно сократило бы время на переналадку при выполнении механической обработки. Г-н Окадзаки согласился на такое изменение.
Приехав на завод в следующий раз, я обнаружил, что установка дополнительного стола завершена. Внедрение такого решения позволило поднять производительность на 40%. И г-н Окадзаки, и я были в восторге от такого результата и поздравляли друг друга с этим достижением, хотя сейчас я сожалею об одной вещи. Если бы я уже тогда сумел осознать всю значимость перевода внутренних операций во внешние, то система SMED была бы разработана лет на двенадцать раньше.
Третий эпизод
В 1969 г. я посетил цех корпусных деталей на главном заводе Toyota Motor Company. Начальник участка г-н Сугиура сообщил мне, что они переналаживают 1000-тонный пресс в течение четырех часов, хотя фирма Volkswagen в Германии производит переналадку подобного пресса за два часа. Г-н Сугиура получил четкое указание от руководства уложиться даже в меньшее время.
Совместно с мастером и директором завода мы начали искать решение проблемы. Мы занялись четким разделением действий на внутренние и внешние, пытаясь оптимизировать их по отдельности. Через шесть месяцев нам удалось сократить время переналадки до полутора часов.
Мы все были очень довольны таким успехом, но когда я снова зашел в цех через месяц, у г-на Сугиуры была для меня интересная новость. Руководство приказало ему снизить время переналадки до трех минут! Какое-то мгновение я был оглушен. Но затем появилось вдохновение: а почему бы не преобразовать внутренние операции во внешние?
Новые идеи стали быстро возникать одна за другой. На доске в зале заседаний я изложил восемь методов сокращения времени переналадки. Используя эту новую концепцию, через три месяца упорной работы мы смогли достичь желанного времени — три минуты. В надежде, что любую переналадку можно осуществить менее чем за десять минут, я назвал эту концепцию SMED. Система SMED была позднее воспринята всеми предприятиями Toyota и продолжала развиваться как один из основных элементов производственной системы Toyota. Сейчас ее использование распространилось по всей Японии и миру.
Г-н Тайити Оно, бывший вице-президент Toyota Motor Company, в июне 1976 г. так писал о SMED в статье «Внедрение мудрости на предприятии» (Опубликовано в журнале Management, издаваемом Японской ассоциацией менеджмента ):
-
«Еще десять лет назад мы старались так организовать производство, чтобы оно максимально укладывалось в обычное рабочее время. Смена резцов, сверл и подобного инструмента переносилась обычно на обеденный перерыв или на вечер. Нашим правилом было менять резцы через каждые 50 деталей. Однако по мере увеличения объема производства за последние десять лет станочники стали жаловаться, что на переналадку уходит слишком много времени. На обрабатывающем центре замена многочисленных резцов и сверл занимала половину рабочего дня. Если смена инструмента производилась в рабочий день, производство приходилось останавливать во второй половине дня, а из-за этого рабочим приходилось выходить на работу в воскресенье.
Это было нерационально. Так как мы хотели проводить и плановый ремонт в рабочее время, мы стали изучать вопрос о том, как максимально сократить время переналадки. Сигео Синго из Японской ассоциации менеджмента пропагандировал «систему смены штампов менее чем за десять минут», и мы подумали, что такая концепция была бы для нас очень полезна. Бывало так, что после того как мы тратили полдня на переналадку, станок работал всего десять минут. Логично предположить, что если переналадка идет полдня, то и производство должно идти как минимум не меньше. Но тогда у нас оставалось бы много лишней продукции, которую мы не смогли бы продать. Сейчас мы рассматриваем возможности сокращения времени переналадки до нескольких секунд. Конечно, это легче сказать, чем сделать. Но как бы то ни было, время на переналадку надо сократить.»
В данном отрывке подчеркивается воздействие сокращения времени переналадки на совершенствование производственной деятельности в целом.
Разработка концепции SMED заняла в общем 19 лет. Она возникла в результате глубокого понимания практических и теоретических аспектов рационализации переналадки. Важную роль сыграло требование Toyota Motor Corporation сократить время переналадки пресса с четырех часов до полутора.
Хотелось бы подчеркнуть, что система SMED основывается как на теории, так и на многолетней экспериментальной практике. Она представляет собой научный подход к сокращению времени переналадки, который можно применить на любом предприятии и любом оборудовании.
ОСНОВНЫЕ СТАДИИ ПРОЦЕССА ПЕРЕНАЛАДКИ
Обычно процедуры переналадки представляются как бесконечно разнообразные, зависящие от операции и типа используемого оборудования. Однако, если проанализировать эти процессы с другой точки зрения, можно увидеть, что все операции переналадки состоят из некоторой последовательности шагов. При традиционном способе переналадки распределение времени обычно соответствует представленному в табл. 3.1.
Таблица 3.1.
Этапы процесса переналадки
Рассмотрим каждый из них подробнее.
Подготовка, постоперационная корректировка, проверка заготовок, инструмента и т. д. На данном этапе идет проверка наличия в нужном месте и пригодности к работе всех материалов и инструмента. В этот этап также включается период после обработки, в ходе которого изделия снимают с оборудования и перевозят на место хранения, время на чистку оборудования и т. д.
Установка и снятие резцов, инструмента, заготовок и т. д. — операции снятия изделий и инструмента после завершения обработки и установки деталей и инструмента для следующей партии.
Измерения, установка параметров, калибровка — все измерения и калибровки, которые надо производить для выполнения производственной операции — центровка, разметка, измерение температуры или давления и т. д.
Пробные прогоны и корректировки. Производятся корректировки после обработки пробного изделия. Чем выше точность измерений и калибровки на предыдущем этапе, тем проще предстоящая корректировка.
Частота и длительность пробных прогонов и корректировки определяются квалификацией инженера-наладчика. Самые большие сложности в операциях переналадки заключаются в правильной регулировке оборудования. Самая большая доля времени пробных прогонов связана с такими проблемами регулировки. Если мы хотим облегчить проведение пробных прогонов и регулировки, надо понять, что наиболее эффективный подход — увеличение точности измерений и калибровки на предыдущем этапе.
Рационализация переналадки: основные этапы
Основные этапы процесса совершенствования переналадки представлены на рис. 3.2.
Рис. 3.2.
Предварительный этап: условия переналадки не делятся на внутренние и внешние
При проведении переналадки по традиционной схеме внешние и внутренние операции не различаются; то, что могло бы производиться как внешняя операция, производится как внутренняя, поэтому оборудование простаивает в течение длительного периода. При внедрении SMED надо очень тщательно изучать фактические условия на рабочем месте.
Наилучшим подходом будет, вероятно, непрерывный анализ производства , выполняемый с секундомером в руках. Такой анализ, однако, отнимает много времени и требует высокой квалификации.
Другая возможность — выборочное исследование работы . Проблема этого варианта в том, что выборочные работы только тогда точно отражают фактическую картину, когда они часто повторяются. Такой метод может оказаться неподходящим, если повторяется мало действий.
Третий интересный вариант — исследование фактических условий в цехе путем интервьюирования рабочих .
Лучший метод — видеосъемка всего процесса переналадки. Он чрезвычайно эффективен, если запись показать рабочим сразу по завершении переналадки. Если дать рабочим высказаться, то это часто дает удивительно четкое, полезное понимание проблем. Во многих случаях такое новое понимание удается применить на практике немедленно.
Хотя многие консультанты выступают за глубокий непрерывный анализ производства с целью улучшения процесса переналадки, на самом деле неофициального наблюдения и обсуждения с рабочими часто вполне достаточно.
Этап 1: разделить действия по внутренней и внешней переналадке
Наиболее важный шаг при внедрении SMED — провести различия между внутренними и внешними действиями по переналадке. Я думаю, все согласятся, что подготовка деталей, обслуживание и т. д. необязательно производить с отключением оборудования. Тем не менее удивительно, насколько часто делается именно так.
Если же провести специальные исследования по переводу как можно большего числа операций с внутренних на внешние, то время внутренних операций, выполняемых при отключенном оборудовании, обычно удается сократить на 30-50%. Таким образом, четкое понимание различий между внутренними и внешними действиями — суть SMED.
Этап 2: преобразовать внутренние действия во внешние
Я только что отметил, что обычно время переналадки можно сократить на 30-50%, если разделить внутренние и внешние процедуры. Но даже такого огромного сокращения недостаточно для достижения целей SMED. На втором этапе — преобразования внутренней переналадки во внешнюю — надо:
-
проверить все операции с целью выяснить, не воспринимаются ли какие-либо действия ошибочно как внутренние; найти способы преобразования этих операций во внешние. Сюда можно отнести, например, операцию подогрева, которая ранее производилась только после начала переналадки, и операцию центровки, которую можно выполнить до начала производства.
Часто удается преобразовать внутреннюю переналадку во внешнюю путем более тщательного рассмотрения ее функции. Крайне важно обозначить новую точку зрения, не связанную старыми привычками.
Этап 3: упростить все аспекты операции переналадки
Хотя иногда путем простого преобразования внутренних действии во внешние и удается уложиться менее чем за десять минут, в большинстве случаев это невозможно. Именно поэтому нужно сначала приложить целенаправленные усилия по упрощению всех элементарных внутренних и внешних операций. Таким образом, на этапе 3 нужен подробный анализ каждой элементарной операции. Следующие примеры говорят об успешном проведении этапов 1, 2 и 3.
- На фирме Toyota Motor Company время внутренней переналадки станка по нарезке болтов, которое ранее составляло 8 ч, было сокращено до 58 сек.
- На фирме Mitsubishi Heavy Industries время внутренней переналадки 6-шпиндельного сверлильного станка, которое ранее составляло 24 ч, было сокращено до 160 сек.
Необязательно выполнять этапы 2 и 3 последовательно, их можно выполнять почти одновременно. Я их разделил, чтобы продемонстрировать два обязательных условия: сначала анализ, затем — внедрение.
ЗАКЛЮЧЕНИЕ
Система SMED разрабатывалась в течение 19 лет на основе тщательного анализа теоретических и практических аспектов совершенствования переналадки. Таким образом, анализ и внедрение служат основой системы SMED, поэтому должны входить в любую программу улучшений.
Есть два вида действий переналадки — внутренние и внешние. Три основных этапа улучшения процесса переналадки включают разделение этих двух видов действий и преобразование внутренних операций переналадки во внешние. Когда это сделано, все аспекты переналадки надо максимально упростить. Улучшения процесса переналадки можно производить на любом этапе.
Глава из книги Сигео Синго "Быстрая переналадка. Революционная технология оптимизации производства" любезно предоставлена издательством